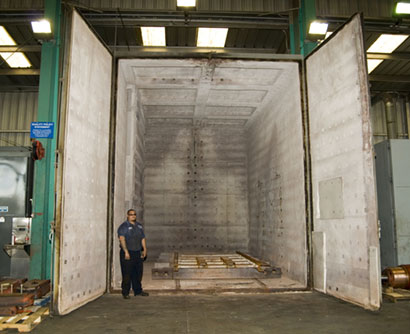
16’ x 21’ x 14’ Burn Out Oven Overview: From cleaning stators and windings to reclaiming coated parts, removing plastics from screws and the safe removal of rubber, Bradleys’ utilizes our Steelman heat-cleaning oven. In our burnout oven, varnish, epoxy, paint, grease, rubber and other combustible materials are removed from metals. Bradleys’ burnout ovens have a high-fire afterburner that breaks down and eliminates any chemical residues or VOC fumes that could be released into the environment. Bradleys makes every effort to protect our fragile coastline. Our goal is to exceed your expectations.
Bradleys’ burnout ovens keep your motors safe. They are specially designed to prevent core damage due to overheating.Core loss occurs when insulation in a stator core is compromised or breaks down. Bradleys’ burn out oven utilizes low oxygen / high temperature burner gases; a unique design that inhibits combustion on the parts of your motor
Bradleys' burn out oven uses a magnetic part temperature probe and temperature controller. These regulate the core temperature and maintain it within five degrees Fahrenheit of the set point. To get accurate oven temperatures, the part temperature controller regulates the primary burner. The part temperature controller also regulates cool water injection, in the event of core-releasing heat or isotherms. Due to these capabilities, the core cannot exceed the desired temperature. This system is interfaced with a cycle timer circuit to ensure process completion, before shutting off. The oven’s chart recorder documents the temperature throughout the burnout oven process. This chart recording is available to the customer upon request.
Combustible vapor in the burn out oven is measured and controlled; maintained at a safe level to prevent fires and meet EASA standards. Rather than sounding an alert AFTER a fire has started, the burn out oven design automatically prevents any fire from igniting, without operator monitoring.